Posts Tagged ‘Modular Construction’
January 19, 2010
Las Vegas – IBS Show – Professional Builder Show Village – Opening Day
Final touches were added everywhere on Tuesday in preparation for opening the gates. Traffic through the homes and at the show in general seems to be up from last year and, fortunately, the rain is holding off!
The La Linda is the perfect combination of Traditional meets Contemporary. The clean design elements and finish out emphasizes the openness of the floor plan and the great use of space throughout this beautiful home.
The Highlander is designed to be flexible enough to work for many different needs and applications. For the show, our Highlander model has been finished out to meet the need for a vacation home on the lake or in the mountains. From the flooring to the slate to the mirrors, no detail was overlooked in conveying that luxury get-away feel throughout this charming cape.
Here are our first pictures as the Design Team puts the final polish on for the guests. Check back soon for more photos and show details as they happen.
Tags:factory-built, green modular construction, home show, housing developers, Innovative design, International Builders Show, Las Vegas, las vegas home show, Modular Construction, modular home, NAHB Home Show, Palm Harbor, Palm Harbor Homes, Professional Builder, Show Village 2010, systems built
Posted in Home Shows, News | Leave a Comment »
March 18, 2009
Working with Palm Harbor Homes as your home construction partner gives you access to all of the advantages we provide our builders to help them achieve their business goals. For over 30 years, we have earned our reputation for delivering customization, quality, value and customer satisfaction with our beautiful modular and manufactured homes. As part of our family of builders, Palm Harbor and Discovery Homes, Nationwide Custom Homes and PHN Commercial Structures combine to make us the only systems built housing company building to HUD, modular, commercial and local building codes from coast to coast. Our history and experience allow us to offer important market advantages for your business.
The Sales Advantage
- Sell MORE with FEWER models.
- Broad product offering targeted to the specific needs and price points of your customers.
- We personalize or customize homes as needed.
- Our ongoing aggressive training equips your team for success.
- Our simplified selling story means your sales team spends more time successfully selling homes and less time specing out homes and writing up orders.
- Palm Harbor delivers the number #1 selling brand name in the United States.
The Marketing Advantage
- Our company web site attracts 175,000+ visitors per month and generates in excess of 3,500 leads per month.
- Palm Harbor and its family of companies routinely market nationally using television, trade publications, regional and national home shows, our own model centers and display models and spec homes that sizzle.
- We can provide you with product brochures, posters and point of sale materials that support the highest levels of professionalism.
The Architecture and Design Advantage
- Displaying our beautiful, eye-catching designs not only increases traffic, but also increases the quality of traffic with higher credit score buyers.
- Our design flexibility allows us to meet the needs of any customer, any code, on any lot with the architectural details and square footage to meet your customer’s desires.
- A home that does not get the consumer emotionally excited will not sell. Our homes deliver the WOW factor. Curb appeal and interior eye appeal abound.
- Architectural, engineering and design services to support your specific needs.
- We build GREEN and can help you with certification for various green building programs – LEEDS, NAHB, Earth Advantage and others.
The SmartPlus Construction Advantage
- We provide the only standard 5-year Protection Plan on all homes – Not an add-on insurance policy.
- Our homes consistently weather the extreme forces of nature.
- We help you create a construction story unique to your market.
- We build our own custom DuraBuilt cabinets for strength and beauty.
- Our years of experience building ENERGMISER® and ENERGY STAR® awarded homes guarantee your customers savings long after the mortgage is paid.
The Gold Key Care Advantage
- We build it. We finish it. We give the keys to the customer.
- Our technicians complete a personal customer walk through and orientation.
- Customers receive our 5-year Protection Plan.
- We provide an 800 number for the Customer to call us for service needs.
The Customer Satisfaction Advantage
- We really want to know the customers’ experience, so we ask!.
- 61% of our internal consumer sales result from referrals.
- Happy, satisfied customers equal MORE sales.
The Financial and Insurance Services Advantage
- Forbes.com Top 10 list in 2007 for our Financial Integrity.
- Publicly traded with strong financials/investment opportunity.
- CountryPlace Mortgage financing services.
- Standard Casualty Insurance services.
Please contact Steve Reyenga, VP of Sales, at sreyenga@palmharbor.com or 800-456-8744 for more information on Palm Harbor builder or retailer opportunities in your area.
Tags:builders, commercial modular construction, construction bids, Custom modular home, factory-built homes, green modular construction, home builder, home for sale, housing developers, huge savings, Innovative design, Modular Construction, modular home builder, Nationwide Custom Homes, Palm Harbor Homes, systems built
Posted in News | 15 Comments »
March 11, 2009
The 2-story, 3,432 sq. foot home built for Masco for the 2009 Professional Builder’s Show Village at the NAHB International Builder’s Show is available now at a huge discount. This 4 bedroom, three bath plus 2 bonus room home is 44’ x 68’ and features every top of the line green building feature and finish out currently available. Here are just a few of the many amazing bonuses and upgrades!
- LP SmartSide Trim & Siding
- Integrated Garage
- Rock Accents
- 84″ Shower with Seat
- Orepac Wood Molding and Trim Package
- Milgard Windows
- Shaw Hardwood Flooring
- Master Closet System
- Traba International Interior Doors
- Butler’s Pantry
|
- Oil Rubbed Bronze Package
- IceStone Solid Surface Counters
- GE Profile Series Appliances
- Home Office Center
- Deceuninck Decking and Railing
- Merillat Cabinets throughout
- CA Modular Approval
- HVAC System
- Sprinkler System
- Click here for complete list.
|
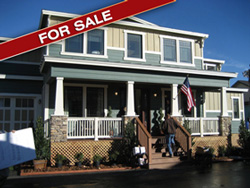
The Capistrano - For Sale!
The Capistrano – Green Building Home by Masco for Profession Builder’s Home Show
Approximately 3,432 Square Feet
2 Story, 4 Bedrooms with two bonus rooms upstairs and 3.5 Baths
Featured as the “Green” home in the Professional Builders’ Show Village, this home focuses on reducing energy consumption waste and it’s resulting carbon foot print like never before. It features the latest in green design and products available.
Slideshow of Capistrano’s beautiful interiors and exterior pictures.
This beautiful home valued at over $700,000 must be moved now! Appraisal will give you instant equity!
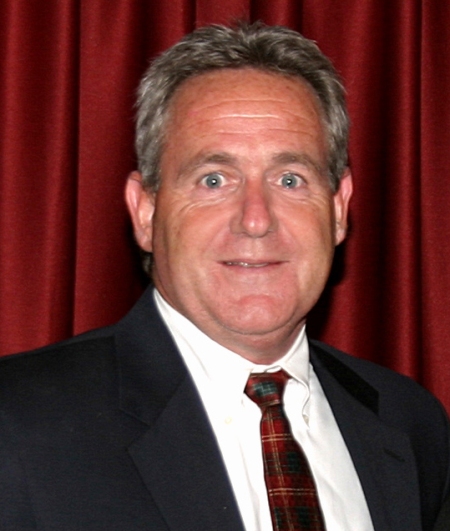
Steve Reyenga
Please contact Steve Reyenga, VP of Sales, at sreyenga@palmharbor.com or 800-456-8744 for more information or to make an offer. This amazing, once-in-a-lifetime value won’t last long!
Tags:Custom modular home, factory-built, green modular construction, home for sale, home show, housing developers, huge savings, Innovative design, International Builders Show, Las Vegas, Modular Construction, modular home, NAHB Home Show, Palm Harbor, Palm Harbor Homes, Professional Builder, Show Village 2009, systems built, temporary class room, training room
Posted in News | Leave a Comment »
January 16, 2009
The NAHB’s 2009 International Builders’ Show is right around the corner (January 20-23). Yesterday, January 15, we kicked off the 5 set days for our three show homes and a school house (click to see details with floor plans and artist’s renderings). This is a mamoth project – 4 homes in 5 days! Here is an up-to-date slideshow of what’s going on at the Show Village right now:
Tags:factory-built, green modular construction, home show, housing developers, Innovative design, International Builders Show, Las Vegas, Modular Construction, modular home, NAHB Home Show, Palm Harbor, Palm Harbor Homes, Professional Builder, Show Village 2009, systems built, temporary class room, training room
Posted in News | Leave a Comment »
April 1, 2008
Bryan Johnson, of Nationwide Custom Homes, was recently honored as one of the Top 30 Under 40 in the Systems Built Industry for 2008. As a recipient of this prestigious award, Bryan is recognized for his outstanding leadership, skills, visibility and influence in shaping the future of housing today.
This award was presented at the Building Systems Councils Dinner at the International Builders’ Show in Orlando, Florida, on February 12, 2008. The award is presented by American Home Bank, N.A., and sponsored by NAHB’s Building Systems Council (BSC), Home Buyer Publications, Forest Homes & J. Rouleau & Associates.
An independent panel of judges is involved in selecting the winners. These judges include Charles Bevier of Building Systems Magazine, Robert Cantrell of Stone Mill Log Homes and Roger Nelson of Anersen Windows.
Rick Baker, Vice President of Sales for Nationwide Custom Homes, stated, “We could not be more proud of Bryan and the outstanding projects he has won and produced in his region. He has been with Nationwide for 1½ years and in our industry for 8. We see great things ahead for Bryan.”
Tags:Best 40 Under 30, Bryan Johnson, Building System Magazine, Building Systems Council, Leadership, Modular Construction, modular homes, NAHB, Nationwide Custom Homes
Posted in News | Leave a Comment »
March 31, 2008
One of the biggest opportunities for maximizing profits in any modular project is the transition from dealer to builder. Without proper planning and coordination, unexpected delays and cost overruns can soak up vital profits on any project. This is especially important in the set. This checklist will help keep your next set on-schedule to keep your costs down.
- Establish a master schedule – Maintain a master schedule with every detail of the project and share it with everyone involved to clearly communicate all expectations and keep everyone on the same page. Subcontractors and inspectors must show up in the right order at the right time. This can be as simple as creating a spreadsheet or using one of many project management software tools that have been created for just such development projects.
- Communicate in advance with your building inspector – Although modular homes are built to the IRC and set to the manufacturer’s instructions, advance conversations with your building inspector will make you aware of any particular preferences your inspector may focus on. Knowing these in advance will help you to be prepared and avoid costly delays.
- Know your transport route – Drive your delivery route looking for complications such as unexpected u-turns, road construction, narrow lanes and even low-hanging limbs. Be sure to communicate these ahead of time with your transport crew. Also, discuss delivery times if commuter traffic may be an issue.
- Check your site again after a rain – Soft ground may prevent the crane and modules from delivering. If necessary, consider the cost of purchasing a load of rock, which will probably be less than having to stop or reschedule the delivery and crane set.
- Create a set map for your site – Every site is different. Plan in advance for the delivery location of the crane and modules to allow for easy access. Some lots are tight and the equipment and modules are large. Preplanning can save costly crane time and moving on your set date.
- Plan for a bulldozer or front-end loader – Once the modules are delivered and removed from the toters, this will be necessary to move the modules around the site.
- Check with your manufacturer for ship loose items – Modular homebuilders supply many materials with their homes, but do not assume that they are all the same. Paint, drywall compound, hardware and appliances are all commonly included items. It is a simple matter to confirm with the builder exactly what items will and will not be supplied with the home. These can add up quickly.
- Keep your eye on the clock – At $300 an hour or more, crane time is money. Forgetting to install the sill plate can become a very costly delay at that price.
- Become your crane operator’s buddy – For the price of dinner, he may be willing to drop by your site in advance and share some insight on how to make your set day go smoothly.
- Be on site the first day – Even with an experienced set crew and preplanning, the most important (and expensive) questions will still come up on the first day of the set. Wrong answers cost time and money.
- Check and recheck for a level foundation – Proper tools like laser or optical levels are essential to insuring a perfectly level foundation. Built to 1/8” tolerances, modular homes require an exacting foundation. And it is very difficult to make on-site adjustments for an unlevel foundation.
- Remember that water damage kills profits – No set day is over until the home is secure and watertight. Have plenty of tarps on hand to protect your home from the rain if that is not possible.
Every experienced modular builder and developer will agree that a quality set done with few delays is the key to keeping profit in your pocket. Preplanning and communication are the basis for every great set and this checklist will help to keep your project on track.
If you have suggestions to add to this list, please post a response below so we can all learn from your experience.
Click Here to see a 2-minute modular home set in action.
Tags:building inspector, crane set, modern modular homes; development, Modular Construction, modular development, modular home set, modular homes
Posted in Modular Construction | 1 Comment »
March 6, 2008
Work is under way on a project replacing blight with 3 houses for people of modest means. They’ve got the land and permits to build the homes and have already started digging. Officials recently began work on three affordable yet stylish houses on Patrick Street. Now they just need to find the homeowners……
Read the full article from the Orlando Sentinel (on February 28, 2008) by Amy C. Rippel
Tags:commercial construction, Florida Real Estate Art in Architecture, Kissimmee, Kissimmee Community Redevelopment Agency, low cost housing, Modular Construction, modular homes, modules, multi-family construction, Nationwide Custom Homes, townhome construction, Work force housing
Posted in News | Leave a Comment »
February 19, 2008
Building Better – The Modern Modular Image
Until recently, the modular industry as a whole has experienced mild resistance because of a lack of education on the process and the product. Many confused this construction method with trailers, mobile homes or manufactured homes. And, truthfully, many in the industry did not help this image by using the term “modular” to market an unattractive, boxy home that looked much like a trailer. Many referred to this as a “HUD-ular.” Not surprisingly, a homeowner or builder planning to build a modular home in a neighborhood could often expect to be met with active protests from members of the community or the planning or architectural committees.
However, in the last few years, much has been done to educate the public about the capabilities of modern modular housing and remove the stigma that had attached itself to the industry. Primarily, the work of talented architects to develop unique and appealing exterior elevations for modular homes that make them virtually indistinguishable from site built. Since 2003, Tony Lucas, Palm Harbor’s own designer, has been putting his years of modular experience to work with builders and developers across the country to create exterior applications and floor plans that are designed specifically for that region, land type, usage and customer lifestyle. As the industry grows, the role of architects will be vital to its maturation and public acceptance as a mainstream home building method.
Public displays in large venues such as the International Builders’ Show have also played an important role in exposing the public and homebuilders to the myriad of applications for modular construction in all types of residential and commercial construction. Features such as elevators, gourmet kitchens, luxury master suites and media rooms are commonplace. In addition, modular construction is adaptable to multi-family construction, reducing the cost per square foot, which is particularly appealing for cities, community planners and developers charged with creating much-needed work force housing.
Today, more and more cities, states, zoning boards and building officials are fluent in the aspect of modern modular construction. In fact, many municipalities look forward to working with modular because of the decreased construction time, decreased impact on the surrounding areas of the community and the increased strength and quality of the product.
Modern modular construction provides increased building efficiencies, decreased construction costs and renewable resources. As developers and architects continue to work with modular builders, the industry will continue to expand its capabilities and, consequently, continue to “improve its image.” This will permanently erase the last remaining areas of resistance due to a perceived lack of quality or architectural appeal and establish modular construction as the modern version of “traditional construction.”
Read more articles in the same series.
Click Here to send us a question about modular construction or tell us about your next project.
Tags:architects, community development; exterior elevations, local building codes, modern modular, Modular Construction, modular homes, multi-family, Tony Lucas, zoning boards
Posted in Modular Construction | 1 Comment »
February 12, 2008
Building Better – By Design
Improved exterior design and interior space are the primary factors to the broader appeal of modulars. With proper architectural consulting, modular construction can be virtually undifferentiated from on-site construction. This adaptability, combined with its affordability, makes modular construction ideally suited for most projects – single family, multi-family, urban in-fill, resort, commercial or workforce housing.
Like traditional stick-built multi-family units, modular multi-family can be up to three stories high without incorporating steel supports. The assembly-line production of factory-built units is particularly well-suited to the narrow, deep units needed for multi-family construction. Similar to single-family housing, multi-family is made by vertically or horizontally stacking the modules. Even the shafts for elevators can be built before the modules are delivered. Because of the savings, code-mandated items such as sprinklers, fire walls and smoke detectors are often installed in the factory and connected between sections on site.
Historically, some have objected to the use of modular construction in urban areas because of its reputation for having a bland, “box-like” exterior appearance. However, working closely with an experienced architect or designer like Palm Harbor’s own Tony Lucas to execute appropriate exterior cues and interior space configuration produces modular homes that blend well with existing construction styles or even conform to mandates from historical societies. As an architect, Tony’s 30 plus years of working with modular construction allow him to work one-on-one with developers to customize floor plans and elevations for their project. These plans and elevations reflect the spirit of the region and support the living patterns of the targeted homeowner. This careful collaboration between an experienced modular architect and builder with the developer is essential to an attractive, successful modular development.
See a few more of Tony’s designs on www.discoverycustomhomes.com and the Bimini and the Glenn Cairn shown at the IBS 2008 show.
Read more articles in the same series.
Click Here to send us a question about modular construction or tell us about your next project.
Tags:affordability, affordable housing, architects, architectural design, commercial building, infill construction, infill housing, modular architect, Modular Construction, modular design, modular homes, multi-family, narrow lot applications, space configuration, Tony Lucas, workforce housing
Posted in Modular Construction | Leave a Comment »
February 11, 2008
Building Better – In a Controlled Building Center
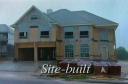
Exposed, rain soaked building sites are common occurances nationwide. And the resulting loss of materials from theft, damage to the exposed areas of the home and the cosmetic coverups that follow are just a few of the many risks that are considered “normal” in new home construction. Consequently, one of the aspects of modular construction that is highly appealing to individual homebuyers as well as developers is that it removes these “normal” risks from the home building process.
Modular construction takes place in an environmentally controlled building center. This translates into fewer mistakes, fewer accidents, the elimination of materials theft, provides protection of all materials from the elements and increased recycling. In addition, the actual construction teams benefit by working each day in a clean, climate controlled building. The result is exactly what builders and developers are looking for: more predictable product quality and delivery schedule. Because materials are never exposed to rain and snow, the modular construction process also protects from “sick building syndrome” that can result from toxic mold.
Modules must be transported to the final home site; therefore, they must be built much sturdier, using about 30% more materials than typical site-built construction. In turn, this construction method results in a tighter, more energy efficient home. With the increased demand for “green construction” and “sustainability,” Palm Harbor’s thirty plus years of building experience allows them to work with builders to reach the desired level of “green” qualification required for each development. The modular delivery and set process is also much more environmentally friendly than traditional construction. It creates minimal construction site impact and virtually eliminates site construction waste with a heavy recycling process in the building centers. And the reduction of subcontractors and the shorter building cycle greatly reduces noise pollution and traffic.
Click Here to send us a question about modular construction or tell us about your next project.
Tags:construction risks, controlled building process, energy efficient construction, environmentally friendly construction, green building, green construction, green modular construction, Modular Construction, modular homes, sustainability
Posted in Modular Construction | Leave a Comment »